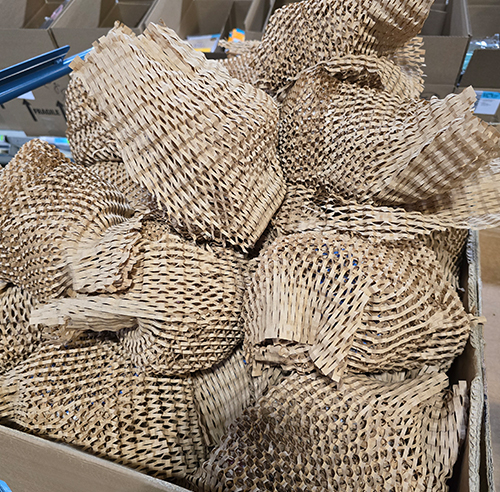
SASB: CG-MR-410a.3
Teams throughout TJX work to implement cost-effective strategies and processes to manage the many different types of waste materials resulting from our operations. We are doing this in several ways, including by eliminating operational waste where feasible and by taking steps to maximize the reuse and recycling of materials in our stores, distribution centers, and corporate offices. These efforts support our global goal of working to divert 85% of operational waste from landfill by 2027.1
Our global approach to managing operational waste includes efforts to:
Maximize reuse and recycling of operational waste, of which the majority is corrugate boxes
Collaborate with our waste-haulers and certain vendors and suppliers on solutions that improve our ability to divert operational waste materials from landfill
Update and enhance our communications on sortation and recycling procedures within certain stores
Address single-use plastics in our operations
Global Operational Waste Diversion Rate:1,2 81%
Our efforts to divert operational waste from landfill in Fiscal 2024 helped to incrementally reduce our reported GHG emissions (Waste Generated in Operations – Scope 3, Category 5) by 5,300 metric tons of CO2e. This represents a 5.6% year-over-year reduction in reported waste-related emissions compared with Fiscal 2023.3
We have many programs across our global business that support our efforts to reuse and recycle our operational waste in our stores, distribution centers, and home offices. Recycling programs for common items, like cardboard, plastic, paper, aluminum, and glass, have been introduced across all of the geographies where we have stores, and we are working to find new ways to reduce and recycle difficult-to-recycle items, like polystyrene.
One of our efforts in this area involves backhauling materials from our stores to dedicated facilities to be recycled or reused. In the U.S. and Europe, we have a number of Asset Recovery & Recycling Centers (ARRCs), which are strategically located within our service centers and have historically served as a central destination for regional recyclable or reusable store material. The majority of our stores in the U.S. and Europe send used corrugated cardboard, plastic film, excess hangers, store fixtures, display cases, and other supplies to their local ARRC, or in certain cases, back to a distribution center, where the items are processed and can be reused in other stores or recycled.
In Fiscal 2024, we continued to accelerate initiatives to increase reuse and recycling rates at our stores, ARRCs, and distribution centers.
One of our focuses in recent years has been to increase the reuse and recycling of corrugated cardboard in the U.S. and other regions. Corrugated cardboard comprises the majority of our operational waste. The ability of our ARRCs and certain distribution centers to accept and process backhauled material, like corrugated cardboard, helps to prioritize its reuse and recycling. In the U.S., a single corrugated cardboard box can be used to deliver merchandise from our distribution centers to our stores up to three times before it is retired and recycled. In the U.S. in Fiscal 2024, over 35.8 million reusable units of cardboard packaging were sent back from our stores through our network of ARRCs to be returned to distribution centers for reuse. For cardboard that could not be reused, our U.S. Associates helped us recycle more than 97,000 tons of cardboard through our ARRC network in Fiscal 2024.
We have efforts in place in certain regions to identify and consider opportunities to remove single-use plastics from our operations and are working with select suppliers to reduce single-use plastic packaging where feasible.
TJX is also working to address single-use plastic merchandise carry out bags within certain geographies. Globally, our stores sell merchandise carry-out bags that are reusable and contain recycled materials.
Certain regions have programs in place to help support the recycling and reuse of merchandise and certain merchandise packaging.
For example, in the U.K. and Ireland, TK Maxx’s long-running Give Up Clothes For Good campaign invites customers and Associates to donate their pre-loved quality fashion and homeware at their local TK Maxx. The pre-loved items are donated to Cancer Research U.K. and Enable Ireland where they are managed for potential reuse. In addition to the donated goods, TK Maxx contributes unsold goods. As of the end of Fiscal 2024, the campaign has donated more than 2.3 million bags of goods, helping to raise millions of pounds for Cancer Research U.K. and Enable Ireland. Read more about this initiative on our Patient Care & Research page.
Additionally, TJX Canada partners with Habitat for Humanity to donate unsold products to people in need. In Fiscal 2023, TJX Canada began partnering with Pact to offer a beauty product packaging collection program at select Winners stores. This program was expanded to all Winners stores across Canada in Fiscal 2024. The Pact program enables customers to drop off used beauty packaging in-store, which is then sent to Pact where it is reused or recycled, as feasible.
Although TJX’s business operations are not water intensive, we believe managing water usage is consistent with both our commitment to environmental sustainability and our low-cost operating philosophy. To that end, we work to monitor our water usage and identify opportunities to improve water efficiency where feasible across our operations. In certain locations, we also utilize collection systems to use water more effectively; for example, at our processing centers in New South Wales, Australia and Sulechów, Poland, we harvest rainwater to supply water to the bathrooms and irrigation systems.
In the supply chain, our TJX Vendor Code of Conduct encourages our merchandise vendors to conserve and protect resources, such as water and energy, and to also take into consideration environmental issues that may impact their local communities. Environmental concerns are incorporated into our merchandise vendor social compliance training materials as well, introducing high-level concepts of environmental sustainability, like water conservation. This training includes specific cost-saving, water conservation recommendations for our suppliers that they may consider implementing at their production facilities. We plan to continue including similar relevant water facts during future training sessions.
At TJX Canada, initiatives led by Associate-run “Go Green” teams have been helping to reduce the operational waste of its distribution centers. In recent years, the “Go Green” teams have helped identify waste reduction opportunities, including installing reusable water bottle refill stations to reduce single-use water bottles, reducing or eliminating single-use plastic bags being used along various stages of operational processes, and replacing bubble wrap pouches for store delivery processes with a curbside-recyclable paper product.
1Where TJX manages the waste operations for the stores.
2Waste figures beginning in FY2022 reflect a change in estimation methodology following several waste audits that enabled TJX to incorporate more accurate estimations. Data figures for FY2022 and FY2023 have been restated.
3Beginning in FY2022, data for this metric reflect a change in estimation methodology for U.S. sites where waste is not weighed as well as the adoption of the U.S. Environmental Protection Agency's published emissions factors for Scope 3: Category 5.
Updated October 2024